Hidden Costs of Forklift Maintenance
Hidden Costs of Forklift Maintenance
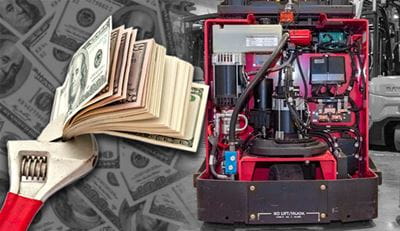
Discover How a Telematics Solution from iWarehouse can Help you Reduce These Costs.
More than ever before, companies are exploring telematic solutions to drive down costs associated with their forklift fleets as well as other material handling equipment. However, many of these organizations are focusing solely on the actual maintenance costs but are not taking steps to ensure ways to avoid these costs all together or minimize them by reducing the amount of time a service provider is on site.
We are all familiar with the traditional labor and parts costs associated with repairing industrial equipment. Essentially the more time a service technician spends working on equipment at your facility the more labor costs are incurred. But what if you could help to reduce the amount of time a technician spends at your facility by providing additional information that will enable them to diagnose your equipment quicker? With iWAREHOUSE, you can.
iWAREHOUSE gives you the ability to help control these costs by reducing the amount of time a service technician spends at your facility through fault code reporting, battery monitoring and schedule maintenance reminders. The following are examples how a properly utilized telematic system like iWAREHOUSE can create maintenance efficiencies and reduce hidden maintenance costs of your material handling fleet.
![]() Fault Code Reporting - This information can be a very valuable tool when it comes to troubleshooting an issue with a forklift and reducing repair times. iWAREHOUSE has the ability to pinpoint potential maintenance issues for a service technician, helping them to diagnosis an issue quickly. Also, when this code is generated, it includes pertinent information including the exact time the code occurred, the current battery state of charge, and who was operating the truck during the time of the code. These capabilities can reduce maintenance costs by reducing the time it takes to repair a truck. For example, once the service technician is on site they will ask as many questions about what exactly the truck was doing when the issue occurred. Based on the nature of large distribution centers, finding out who exactly was on what truck at the time a code came up can be a daunting and time-consuming task. Without having insight into the specific scenario in which the maintenance issue occurred can increase repair times, especially if the issue is intermittent. To take that one step further, if a truck is used by multiple operators but a particular code only occurs with the same operator, it can indicate that the code is induced by an individual's particular operational procedure and may not be truck related at all. Additionally, there is nothing worse than to place a service call which has a service technician come to your facility, bring in all of their tools, work on a truck for over an hour and have the invoice state the technician was "unable to duplicate issue". Regardless if the service technician found an issue or not, the forklift owner will still be on the hook for placing the service call. Ultimately, there are several factors other than a service technician's technical ability that can affect the time it takes to repair a forklift. Utilizing a fault code reporting solution, you can ensure accurate, timely notification of the exact issue to the appropriate individuals, providing as much pertinent information as possible, which will ultimately help ensure the most efficient forklift repair. With labor being a major portion of overall maintenance costs, being able to reduce those costs will have a significant impact to your bottom line. |
![]() Battery Monitoring - This is by far one of the most significant cost saving measures for reducing the hidden maintenances costs associated with a forklift. Oftentimes an issue that seems to be related to the forklift its self is actually caused by the battery within it. Two primarily drivers are batteries not being charged or not being watered properly. These battery issues can lead to mechanical and electrical malfunctions in a forklift, however many times they are easily addressed if you have the right data. Those unwarranted maintenance costs can be virtually omitted by implementing a telematic battery monitoring system. |
With the capability to monitor a truck hour meter down to the tenth of an hour, and having the ability to automatically notify the proper personnel of when the proper time has occurred to perform maintenances will increase efficiencies in the scheduling of the work itself and better manage downtime when it occurs. It can also reduce instances of having equipment having too many maintenance intervals, based on usage accumulation. In short, by having the ability to utilize automatic alerts of schedule maintenance reminders will create additional maintenance efficiencies and help reduce overall forklift costs. |
There is no question that the more information you have the better. A telematics system such as iWAREHOUSE can provide you the data that will enable your service technicians to repair your equipment faster and with a higher level of accuracy which saves you maintenance costs but more importantly it reduces the amount of downtime associated with your forklift fleet.