Forklift Applications: Choosing the right forklift for your application
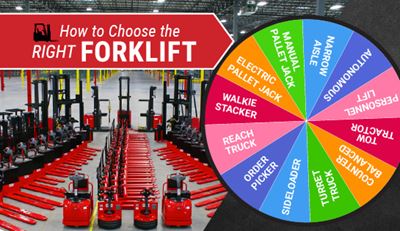
Do you know what type of lift truck is right for your needs? We take a look at the variety of industrial lift trucks and warehouse vehicles and their intended applications to help you select the most efficient vehicle for your operation.
A Solution for all Fleets
Distribution centers, warehouses and manufacturing facilities fall at the crossroads between two converging demands: increase capacity to store more materials, and move these materials faster than ever before. Increasing capacity isn’t always as easy as constructing more warehouse space, and more often takes the form of requiring higher storage density (storing more materials in the same amount of space). Likewise, increasing handling speed isn’t solved by simply throwing more labor at the issue, and especially not if there is less space to work in as the result of increasing density.
When solving these challenges, an often-overlooked piece of the puzzle is the warehouse’s fleet of material handling trucks and equipment. A wide variety of different, application-specific forklifts exist on the market, each engineered to serve a unique purpose. With a few changes of equipment, the above density and velocity challenges can be directly mitigated, creating conditions where such challenges suddenly become opportunities to do even better!
In this article, we’d like to outline the full array of commonly available industrial forklifts and warehouse vehicles, along with describing their intended applications. Readers might find that long-accepted problems within their spaces have solutions after all, such as using personnel lifts instead of rolling ladders to free up aisles, or turning to walkie stackers instead of full forklifts in order to save maneuvering space. Better yet, perceived limitations within your space might turn out to be readily solvable, paving the way for density and velocity increases to suit.
We’ve categorized lift types below by their general operational features, but please note, these categories should not be confused with technical or regulatory classifications of lift trucks. We’ll add a bit of clarification on this point at the end of the article. With that, let’s jump into the first category of lift truck types: manual lifts.
Manual Lifts
When we refer to a lift being ‘manual’, we are indicating that some or all the physical effort needed to maneuver the transported materials is performed by an operator using their body as the source of power to do so. When done safely and carefully, manual lifts are excellent solutions for moving materials in low volume, infrequent, or odd-size formats.
-
Manual Pallet Jack
Making up the simplest options in our list of equipment, a Manual Pallet Jack relies on a human operator to physically maneuver materials to their destination. That is to say, manual pallet jacks do not have driving capabilities, though some are available with electric vertical lift capabilities used to pick up heavier loads off the ground.
Manual pallet jacks can be found in virtually every warehouse that handles palletized materials, serving as either the primary equipment for low volume use, or as a backup in a high-volume operation. Pallet jacks are only able to move materials around at floor level and are not used to elevate materials to racking or shelf heights. -
Motorized Hand Truck
Stepping up slightly from a manual pallet jack, a Motorized Hand Truck (also known as a powered pallet jack) replaces the human operator with an electric motor as the maneuvering force. Electric pallet jacks substantially improve the ergonomic factors involved in moving large material pallets, driving themselves with the push of a button.
The remaining manual element is simply that the operator needs to walk with the truck and steer with their arms – the electric travel and lift motors do the rest. Similar to manual pallet jacks, motorized hand trucks can only elevate pallets several inches off of the ground, ideally used for moving heavy, high-volume materials around at ground level. -
Walkie Stackers
Where pallet jacks and hand trucks fall short in their inability to lift materials vertically, Walkie Stacker Trucks save the day by adding vertical lift capabilities onto a motorized hand truck base.
Used to elevate materials under the guidance of a human operator steering the wheels, a walkie stacker is an economical option for low to medium volume operators that do not require a full driven forklift. Further, the smaller footprint of a walkie stacker can be beneficial for parking the truck unobtrusively near production areas, ready for infrequent heavy stacking or lifting needs.
Rider Trucks
Our next category of material handling lifts, referred to as Rider Trucks, utilize powered travel and lift motors to transport goods, and place the operator in a standing position behind the materials being moved. We typically differentiate a “ridden” lift as one with a standing operator, whereas a “driven” lift (covered in the next section) sees the operator seated. Rider trucks are ideal for smaller footprint, narrow aisle, lighter weight applications, especially where operators need to exit and enter the truck often.
-
Reach Trucks
As the most common lift truck found in warehouse and distribution environments, Reach Trucks are ideal for high-volume, high-density storage applications. Reach trucks are designed for narrow aisle width and very high rack elevations, and are defined by their articulating forks that can ‘reach’ into a rack to set or pick pallets.
This unique extension capability works with rack designs that are 2, 3, or more pallets deep, which cuts down on the amount of traffic aisles needed between stored materials, and in turn increases overall storage density. -
Order Picker Trucks
Order Pickers are specifically designed for a standing operator to quickly travel into their multi-tier storage warehouse and pick individual units to build mixed orders. Most often, an orderpicker will be fitted with an open tote or container on a pallet, which the operator will fill by picking items from various bin positions throughout their warehouse, and then bring back to a pack station to assemble the order.
The operator platform raises up to rack elevation along with the attached container or pallet, allowing for parallel picks in narrow aisles without needing to turn the truck. A pick truck is uniquely intended for pulling materials from stock, and not for putting pallets or smaller packages into stock. -
Sideloaders
Simply put, Sideloader Trucks are designed to move long, very heavy, bulky materials. Pipe, carpet, lumber, building material rolls, roofing panels – anything long and oddly-shaped (usually without a container)- is a good candidate for transporting with a sideloader.
Operators stand behind and off to one side of these trucks not only to reduce the length of the truck (as they’re already quite wide to accommodate their intended materials), but also to provide clear visibility over these materials. Sideloaders are able to elevate materials, and are best utilized to stack large material groups, such as lumber piles and equipment crates.
Driver Trucks
Driver trucks are ideal for heavier, more physically stable, long operation time applications. Most readers will immediately picture a common forklift as an example of a driven forklift vehicle, but there are several more variants worth mentioning as well.
-
Turret Trucks
Maximizing storage density is the primary objective in distribution centers today. Even through the reach trucks described above allow for using pallet racks that are multiple pallets deep, they still need enough aisle space to turn the truck to face the rack when picking. Turret Trucks improve density even further by rotating the pallet and forks on a pivot point in front of the lift, avoiding the need to turn the base of the lift itself.
With turret trucks now only needing to travel straight down rack aisles without turning, these aisles can be further reduced in size, and more pallet racks can be installed in the saved space. Another feature of a turret truck is that the operator’s control station elevates with the forks, allowing for multi-level order picking and precise pallet positioning in the air. -
Counterbalanced Trucks
Otherwise known as a typical forklift, Counterbalanced Trucks are most commonly configured as sit-down driven lifts intended for heavy, high-volume material handling for long periods of time. The definitive feature of these types of lifts is the weight mass added to the end of the vehicle known as a counterbalance, which allows for ample stability in handling and maneuvering loads at moderate speeds and high elevations.
The more counterbalance mass, the higher and faster a lift can go without tripping over. Counterbalance trucks are found in every material handling application imaginable, largely due to their versatility and many available configurations. These lifts are defined by their large counter-weight, not necessarily by their sit-down operation – that is to say, some counterbalance trucks are configured for standing and / or walking operators.
Other Notable Lifts
We’ll conclude our list of fork truck applications with three additional vehicle types that don’t fit into the above standard categories.
-
Tow Tractors
Found in many distribution center applications, Tow Tractors are ridden vehicles used to pull connected carts or bins during order picking, material transportation, and maintenance hauling.
These tractors most often serve a similar purpose as Orderpickers, transporting an employee to pull materials from stock in the warehouse, place the materials into a towed cart, and continue this process to build a mixed order. Another example might more readily come to mind: many airports and train stations use tow tractors to haul luggage and supplies from storage centers out to each point of use. -
Personnel Lifts
Where all the other lifts in our list are designed to primarily move materials, Personnel Lifts are instead designed to (you guessed it) move people. Personnel lifts are intended for use in place of common ladders, scaffolds, and staircases, here elevating employees up to storage racks in a safe and reliable way. Operators stand inside of the personnel lift’s cage, clip off their fall restraint harness, and are quickly elevated up to storage containers to check or pick small items. Once lowered down, employees may choose to leave the lift in a common location or guide the lift to the next location to repeat the process.
Personnel lifts are easily pushed between locations and are not driven (not to be confused with their larger variants found in construction and maintenance industries known as Aerial Lifts, which are driven between locations and intended for much higher elevations). -
Autonomous Lifts
Also known as Automated Guided Vehicles (AGVs), Autonomous Lifts are computer-controlled variants of nearly any model truck described above that can automatically travel, lift, place, and position materials without the need for a human operator. This intelligent technology introduces an incredible range of possibilities for modern material handling businesses, from reducing labor cost to improving safety, increasing pick speed to cutting pick errors, and so on.
Efficiency maximization is the current hot topic in deploying automated vehicles, creating workflows where employees work parallel to AGVs, which combines human subjective problem-solving capabilities with automatic material transport between human workstations.
A Note on Fork Truck Classifications
We mentioned earlier in the article that our fork truck classifications describe operational features, not technical or regulatory features. To further explain this, we want to make sure that readers are clear that OSHA and other safety bodies use a different classification system for categorizing these vehicles by their level of safety risk. When it comes to OSHA-compliant safety training on fork truck equipment, the below classifications are the OSHA categories to keep in mind.
We point this out only to make sure readers understand that while certain lifts might be similar in function or operation, they may fall under separate OSHA classifications and in turn require different training, certification, or qualification to operate. Please be sure to check with your local safety authorities before investing in unique equipment for your facility, to confirm that existing training will apply to your operators, or if supplementary training will be required.
OSHA’s classification list is below, and more information on fork truck safety (along with diagrams of each type of lift) can be found on their website:
- Class I : Electric motor rider trucks
- Class II : Electric motor narrow aisle trucks
- Class III : Electric motor hand trucks or hand/rider trucks
- Class IV : Internal combustion engine trucks (solid/cushion tires)
- Class V : Internal combustion engine trucks (pneumatic tires)
- Class VI : Electric and internal combustion engine tractors
- Class VII : Rough terrain forklift trucks
#forklift #forklifts #raymondforklift #lifttruck #electricforklift #typesofforklifts #pallettruck #manualforklift #narrowaisleforklift #forktruck