Pallet Racking Types
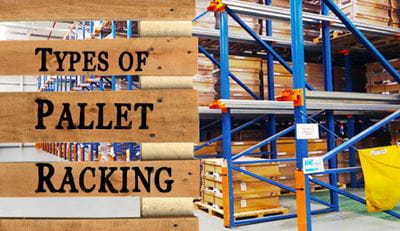
If the last few years have been any indicator, the future for industrial manufacturing clearly seems to be ‘do more with less’. Warehouse, Distribution and Manufacturing spaces are especially under pressure to increase volumes, throughput, and flexibility, driving the need for a fresh take on storage solutions that address these challenges. To help supply chain business owners weigh their options, we’ve prepared the following article on pallet storage racking types and their key selection factors.
Approaches to Warehouse Pallet Storage
Material handling system designers balance a huge array of metrics when designing storage solutions, and nearly every project is unique to each client’s specific business needs. Everything from storage volumes, traffic rates, SKU and lot quantities, inventory turnover, and even perishability comes into play. Of course, commercial elements enter the equation as well including CapEx cost, operating cost, return on investment, installation / construction timeline, and regulatory compliance review (such as for seismic and fire protection elements).
Putting all of this together can be a substantial design effort, but by using qualified partners and focusing on the most important business objectives, owners can easily navigate the process of selecting a racking system that achieves their goals. In fact, the process can even be enjoyable and provide strategic value, illuminating key operational metrics that owners can convert into actionable opportunities.
In starting a new pallet storage project, we suggest that owners spend time developing and defining their goals in terms of the below four key design points. These factors will set the stage for the design work to come, and a good designer will be able to immediately narrow down ideal options specifically addressing these factors.
-
Density
Space efficiency is a primary driver of pallet racking design. You only have so much space in your warehouse (both in square footage area as well as height), and using it efficiently involves deciding on how you use your floor space – either for pallet positions, forklift aisles, workspace, or other material handling equipment. The greater the pallet density, the more storage positions you can fit into the same warehouse space, though at the cost of simplicity and flexibility. Higher densities are usually driven by high volume, low SKU count applications. -
Selectivity
Selectivity refers to how much instantaneous access you require to any individual pallet stored in your warehouse. For example, if you need the option to pull any pallet immediately with the absolute minimum amount of time sorting through other pallets, only a few racking styles would be suitable. High selectivity is a good fit in low volume, high SKU count applications. -
Velocity
Pallet movement rates into and out of the warehouse are another key factor in selecting a warehouse racking design. Pallets that sit for long periods of time need a different degree of access than pallets that move in and out rapidly. Most businesses do not have a singular velocity, but instead have a whole spectrum of velocities based on their product mix. In other words, some products move faster than others, and for this reason we often find mixed racking solutions in the same warehouse, selected to accommodate these different velocity rates. -
Flexibility
While manufacturers tend to have a very consistent inventory scheme, distributors and resellers tend to have highly dynamic inventory schemes. This translates into flexibility needs, and is an import factor in selecting racking designs. Further, flexibility can be more or less difficult to provide depending on the nature of the expected inventory changes. For example, changes in SKU makeup may have little impact if the total pallet inventory count remains the same, whereas changes in pallet sizes and weights may require substantial physical modifications for racking sized for smaller loads.
A fifth design factor that goes without saying is cost. Owners should let their warehouse partners know of their budget target as early as possible, which allows for the right mix of performance factors to be weighed against costs from the very beginning.
There are many more details that point to any given racking solution over others, such as inventory control software complexity, forklift types and costs, reliability and uptime factors, operating and maintenance costs, building heights, regulatory codes, and more. The above main factors are the starting point, and owners are encouraged to engage a trusted design partner to continue the conversation.
Pallet Racking Types
With the above design factors in mind, read on for an overview of the most common pallet racking solutions found in today’s material handling warehouses.
-
Single Deep Pallet Rack
Also known as Selective Pallet Racking, Single Deep Racking serves as the entry point into warehouse storage racking systems. With multiple levels of pallets placed vertically on a simple steel rail structure, warehouse storage volumes can be increased dramatically in the same square foot area. Single Deep racking is typically the least expensive rack solution, but is also the least space-efficient as it requires forklift aisles along every pallet position. -
Double Deep Pallet Rack
With Double Deep Racking, pallets can be stored ‘one in front, one in back’ within the same rack structure. One forklift aisle allows for accessing two pallets per storage position facing the aisle (as opposed to only one pallet per storage space with Single Deep Racking), increasing overall space efficiency. A special forklift type (or attachment) must be used which can extend to reach the rear pallet position. -
Mobile Pallet Rack
This racking system utilizes motorized pallet rack structures to collapse and expand forklift aisle spaces. Mobile Pallet Racks move along guide tracks embedded in the floor slab, with each rack able to nest up against the next rack section when access is not needed, and to open up an aisle lane when access is needed. Advanced safety, access control, seismic restraint, and inventory tracking features are often provided with Mobile Pallet Racking. -
Pallet Flow Rack
Pallet Flow Racking or Gravity Racking systems use heavy-duty rollers installed along declining lane rails, allowing pallets inserted on one end to flow by gravity down to the opposite end of the lanes. Pallet Flow Rack provides ‘deep lanes’ of stored pallets, requiring fewer forklift aisles and more pallet storage positions (typically 4 to 20 pallets deep). This system provides natural First In, First Out (FIFO) storage, great for perishable products. -
Push Back Pallet Rack
Similar to Pallet Flow Racking’s deep lanes of storage and passive gravity flow, Push Back Pallet Racking provides high storage capacity but is accessed from only one end instead of both ends. Pallets are set on nested sleds which slide back when a new pallet is inserted, and slide forward when a pallet is removed. This system provides natural First In, Last Out (FILO) storage, great for commodity materials that are not production-date sensitive. -
Drive-In Pallet Rack
Drive-In Pallet Racking is similar to Push Back Racking above, however instead of using sliding carts to push pallets back into their deep lanes, a forklift is instead used to drive into each lane and physically set each pallet in position. This system offers simpler construction, and is ideal for loads that should not contact each other, FILO storage schemes, and high volumes of similar products. However, the risk of forklift impacts is much higher. -
Deep Lane Shuttle Rack
Offering the high-density benefits of Drive-In Racking above but without the risks of forklift impacts, Deep Lane Shuttle Racking utilizes motorized shuttles to ferry pallets into and out of their storage positions. Forklifts set pallets at the end of each lane, and an automated shuttle then picks up and moves pallets from there. Forklifts will physically move shuttles from lane to lane as needed, allowing for a semi-automated, deep lane, space efficient scheme. -
AS/RS Automated Pallet Rack System
Automatic Storage and Retrieval Systems (AS/RS) are the pinnacle of high density, high volume, high throughput solutions for today’s modern warehouses. Automated conveyance and transport machinery move, store, and pick pallets governed by advanced warehouse management and control systems. Systems may utilize multiple technologies such as stacker cranes, elevating lifts, roaming shuttles, autonomous vehicles, and more.
Associated serves the Upper Midwest’s Material Handling market with Integrated Supply Chain Solutions, Warehouse and Distribution Operation Optimization, Lift Truck Fleet Management, and Consulting Engineering services. We assist customers onsite and remotely from our Addison, IL corporate office and five regional branches near you. For more information or to discuss your Material Handling project needs, please visit our website here, or contact us at [email protected] or (800) 755-7201.
#racksafety #rackstoragesystem #palletrack #palletrackshelving #racking