Types of Material Handling Equipment
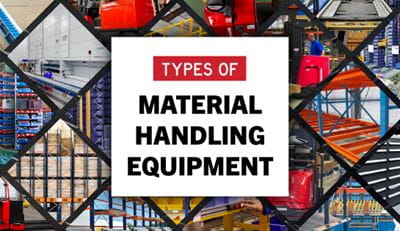
Associated University provides a breakdown of material handling equipment in easy-to-understand groups, including cutting-edge technologies that blur the lines between hardware, software, and heavy machinery.
Material Handling Equipment... it is so much more than forklifts!
When we discuss material handling equipment, what typically comes to most peoples’ minds first is a narrow range of industrial trucks and conveyance equipment. Spending a moment to imagine the warehouses we’ve been in recently, more and more equipment types come to mind, and we’re sure there are even more we’re forgetting. The world of industrial material handling equipment is ever changing, constantly expanding to include new variations of older technologies and brand-new emergent solutions as well. As the catalog of everyday equipment grows over time, most of us could use a quick refresher on the available warehouse equipment on the market today. In this article, we'll provide a contemporary breakdown of material handling equipment in easy-to-understand groups, including cutting-edge technologies that blur the lines between hardware, software, and heavy machinery.
Vehicles and Transport Equipment
By definition, industrial material handling involves moving a high volume of goods between manufacturing and distribution stops as they progress across a supply chain, calling for all different styles of equipment along the way. Between these supply chain stops, freight trucks, rail cars, cargo airplanes, and seafaring ships transport materials en masse. At each stop, materials are unloaded and stored within distribution facilities before continuing on to end users. Whether loading mass cargo vessels or a material handling facility, various single unit handling equipment pieces or forklifts are used to transport goods, such as:
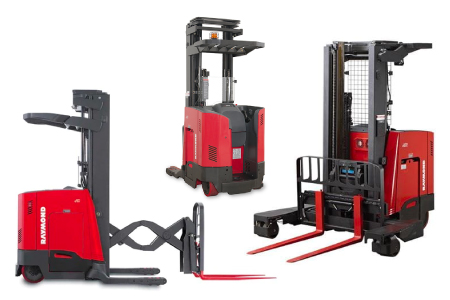
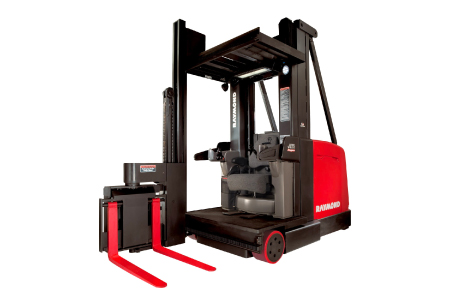
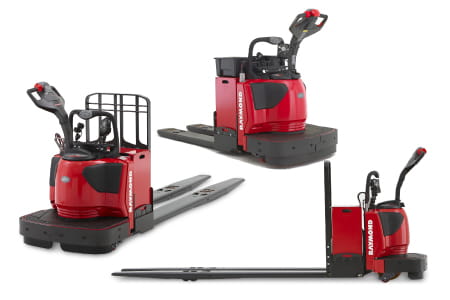
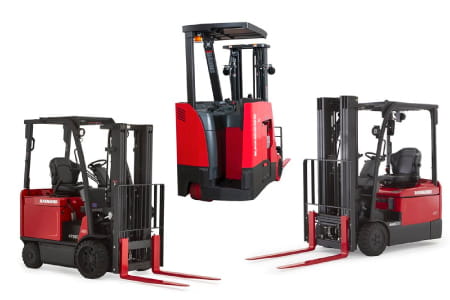
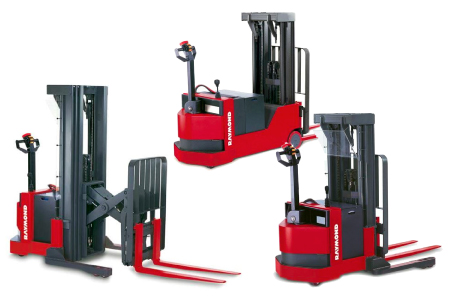
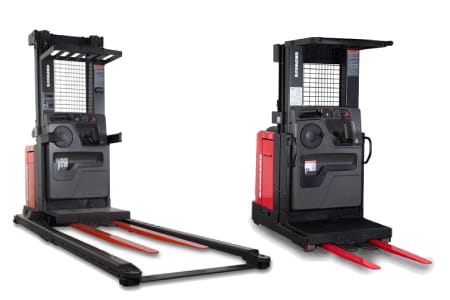
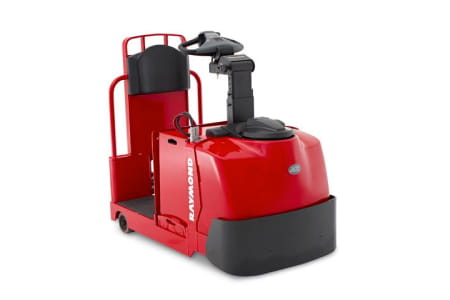
Fixed Storage Equipment
Between distribution legs of their journey, goods are staged and stored in Warehouses and Distribution Centers. These distribution facilities are massive industrial sites, often measuring 250,000 to over a million square feet - this equates to over 22 acres of land, or nearly 20 football fields, of product storage! Within these facilities, storage density is paramount, calling for tightly spaced, tall storage solutions to pack as many goods in as little space as possible, such as:
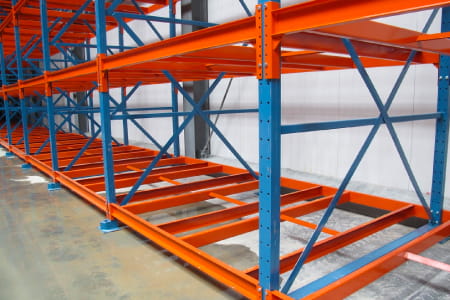
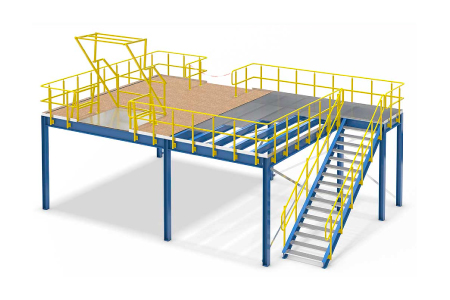
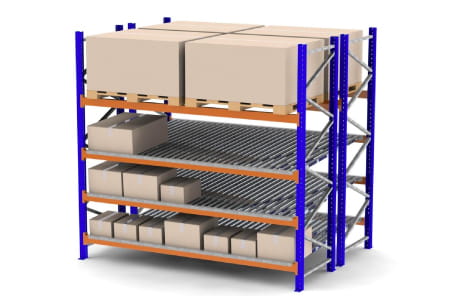
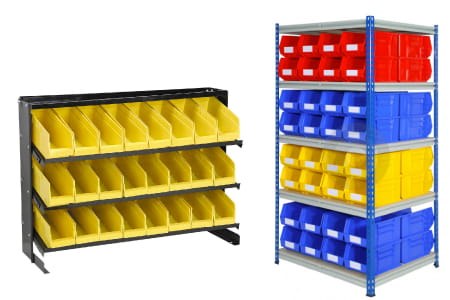
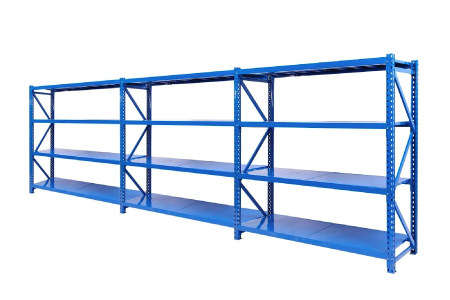
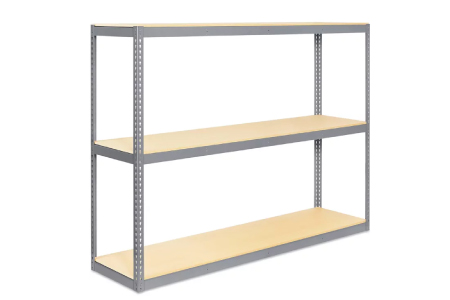
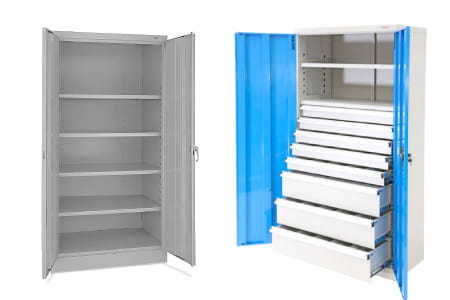
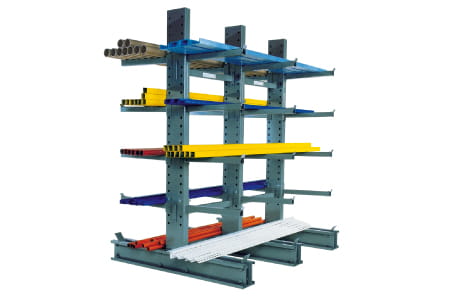
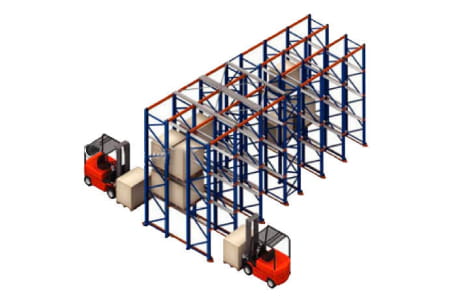
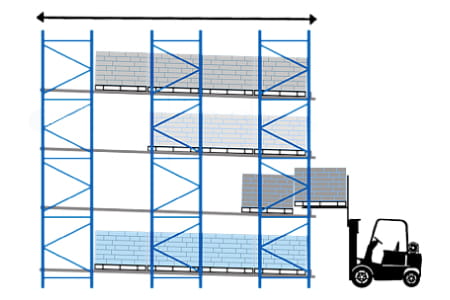
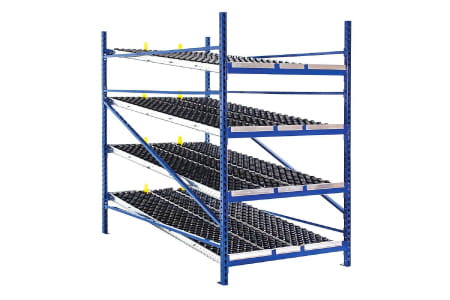
Automated Components
Individual work tasks can be made easier, faster, and safer to complete by using automated components, especially for laborious and repetitive tasks. Simple tasks such as conveying boxes across a warehouse, or complex tasks such as breaking down and repacking bulk containers into individual product packages, are all fair game for tackling through automated machinery. Common equipment components that can be automated to replace manual human labor include:

- Mechanical Conveyors
- Elevators
- Accumulation Tables
- Shrink Wrappers
- Tapers
- Labelers
- Pick Stations
- Deposit Stations
- Repack Lines
- Packaging Lines
- Palletizing Lines
- AGVs (Autonomous Guided Vehicles)
Automated Systems
When multiple individual work processes are automated, the aggregate collection of equipment becomes a system, each piece working together in sync. In material handling, full systems typically take the form of automated storage solutions, such as Automatic Storage and Retrieval Systems (also known as an AS/RS).
An AS/RS uses automatic vehicles, conveyors, elevators, and special racking structures to store pallets or containers. A modern AS/RS can receive goods directly from a manufacturing line, convey containers to storage positions, put these away for weeks or months without losing track of their locations, and then pull and convey those goods directly out to shipping truck docks when ready to leave the facility. All of this can occur without human interaction, at speeds that would otherwise take a large workforce and much more space to complete (since you don't need the space for manned forklift lanes). Separate from these fully-automated systems, lower-cost alternatives are available as semi-automated systems, where human labor and mechanized equipment share the workflow. Semi- and Fully-Automated system examples include:
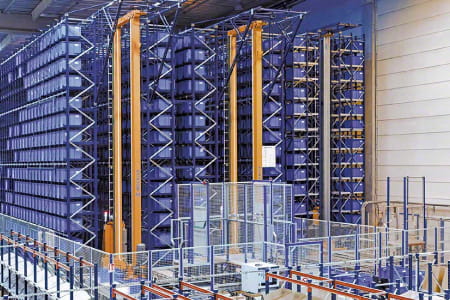
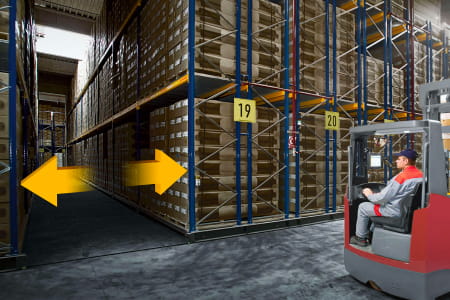
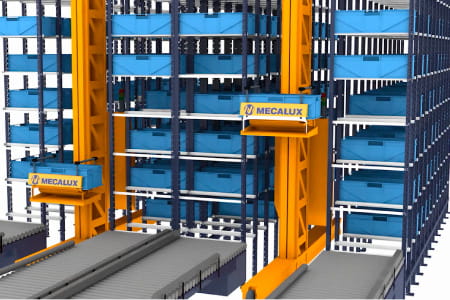
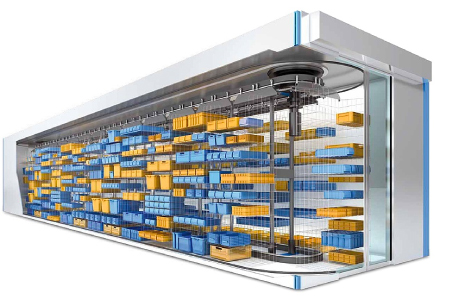
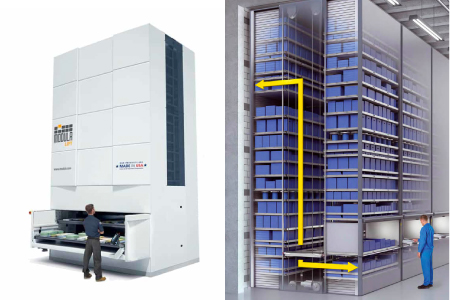
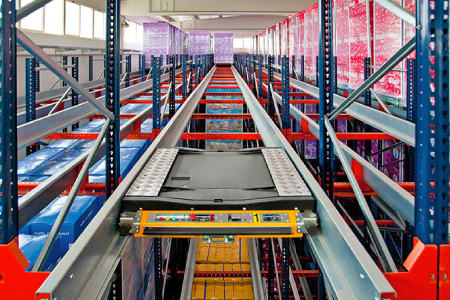
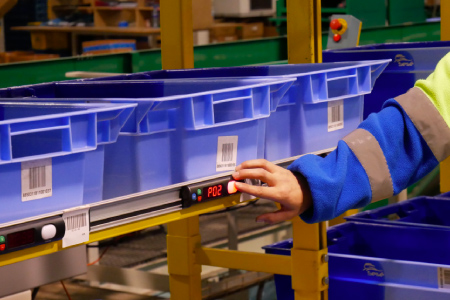
Integrated Technologies
It's hard to imagine, but cutting-edge technological advances are pushing the limits of material handling automation out even farther than the fully automated systems described above. Today, predictive manufacturing, augmented reality, and data analytic systems are creating wider automaton opportunities to integrate workflows for a fully coordinated scheme. Software, hardware, equipment, and employees are all coordinated in real-time, producing ultra-efficient distribution workflows. The lines between what we traditionally understand as task-supporting equipment are blurred as physical gear melds with digital technology that we cannot see, but are functionally an extension of that equipment’s ability to perform. Examples of emerging integrated technologies include:
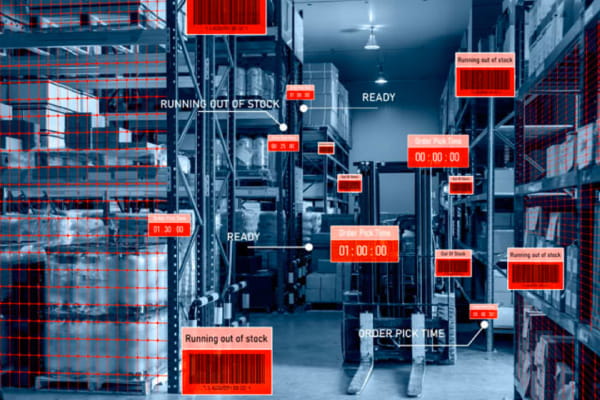
- Augmented Reality
- Digital Twin Warehouse Models
- Warehouse Simulation-Based Planning
- Predictive Logistic Planning
- Automatic Inventory Ordering
- Automatic Order Fulfillment
- Supplier/Distributor Data Integration
- Warehouse Management & Control Software Systems
- Wearable Devices
A Note on Compatibility
Storage Equipment and Handling Vehicles are very closely co-dependent, as specific types of vehicles only work with specific storage structures. For example, reach-type forklifts are required to place and pick pallets in double-deep pallet racking, but would be too large to fit in the tight clearances required by drive-in racking. Buyers should be sure to check compatibility between their vehicles and storage equipment selections early in the design process.
Different industries require different variations of equipment as well. For example, a forklift considered standard in a dry warehouse environment is quite different from the standard choice in a marine dock loading environment. We point this out to say that while our categories here are generalized and wide-reaching, there is a mountain of application-specific detail hidden within each family of equipment. Further, many specific regulations and compliance requirements are enforced where safety and product integrity are paramount, causing more complexity in selecting permissible solutions. For more information on equipment suitable to your exact needs, please don't hesitate to contact us.
#automatedmaterialhandling, #forklifts, #materialhandlingequipment, #palletracking, #warehousestorage