Forklift Battery Safety: Essential Practices for a Safe Workplace
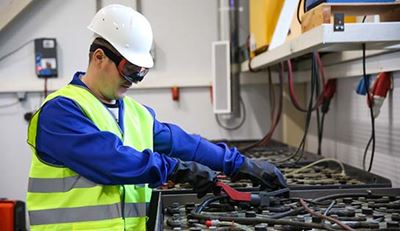
Forklift batteries can weigh thousands of pounds, contain corrosive chemicals, and emit flammable gasses, and they should be managed with as much vigilance and caution as forklifts themselves.
For most businesses, forklift safety is something that is taken very seriously. Forklift accidents can often result in serious injury or death, and there are many training programs for both forklift operators and warehouse pedestrians.
One aspect of forklift safety that is often overlooked, however, is battery safety. Forklift batteries can weigh thousands of pounds, contain corrosive chemicals, and emit flammable gasses, and they should be managed with as much vigilance and caution as forklifts themselves.
Proper Training and Education
The foundation of forklift battery safety is proper training and education. All personnel involved in handling, charging, and maintaining forklift batteries should receive comprehensive training. This training should cover the basics of battery operation, battery handling, potential hazards, and emergency procedures. Employees should be well-versed in the manufacturer’s guidelines and safety protocols to minimize the risk of accidents.
Personal Protective Equipment (PPE)
Handling forklift batteries involves exposure to hazardous materials, including sulfuric acid and heavy metals. To protect against these dangers, employees should always wear appropriate personal protective equipment (PPE). This includes acid-resistant gloves, safety goggles or full-face shields, long sleeves, long pants, close toed shoes and aprons. PPE acts as the first line of defense against chemical burns, spills, and other potential injuries. Additionally, employees should never wear any metal jewelry or have metal tools strapped to their bodies when handling batteries.
Ventilation and Venting
Lead acid forklift batteries emit hydrogen gas during charging. Inadequate ventilation can lead to the accumulation of this highly flammable gas, posing a significant explosion risk. Make sure that the charging area is well-ventilated to disperse hydrogen gas effectively. In addition, battery charging stations should be equipped with proper venting systems to prevent gas buildup.
Safe Charging Practices
Charging forklift batteries is a routine but critical task that requires strict adherence to safety protocols. Here are some key practices to follow:
- Use a Designated Charging Area: Establish a designated area for battery charging, away from open flames, sparks, and other ignition sources. As previously mentioned, the designated charging area should be well ventilated.Many operations have a dedicated charging room for this purpose.
- Check All Connections: Ensure that the charger is compatible with the battery and that connections are secure. Loose connections can cause sparks and overheating.
- Pay Attention: Regularly monitor the charging process to look for anything unusual, such as excessive heat or unusual noises. If any issues arise, stop the charging process immediately and investigate.
- Avoid Overcharging: Overcharging can lead to excess gas, overheating and battery damage. Use chargers with automatic shut-off features to prevent overcharging.
Regular Maintenance and Inspection
Routine maintenance and inspection are crucial for ensuring the longevity and safety of forklift batteries. Implement a regular maintenance schedule that includes:
- Cleaning: Keep battery terminals and connectors clean and free of corrosion. Use a mixture of baking soda and water to neutralize any acid spills.
- Checking Electrolyte Levels: For lead-acid batteries, regularly check and maintain electrolyte levels. Add distilled water as needed, but never overfill.
- Inspection: Conduct visual inspections for any signs of damage, such as cracks, leaks, or bulging. Address any issues promptly to prevent further damage or safety hazards.
Safe Handling and Storage
Proper handling and storage of forklift batteries are essential to prevent accidents and ensure their longevity. Follow these guidelines:
- Use Lifting Equipment: Use appropriate lifting equipment, such as battery lifting beams or cranes, to move heavy batteries. Never attempt to lift a battery manually.
- Store Batteries Properly: Store batteries in a cool, dry, and well-ventilated area. Avoid exposure to extreme temperatures, which can affect battery performance and safety.
- Keep Batteries Upright and Secured: Make sure stored batteries are always upright, and anchor batteries in place to prevent tipping or falling, which can cause spills and injuries.
Emergency Preparedness
Despite all precautions, accidents can still happen. Being prepared for emergencies is crucial for minimizing harm. Ensure that your workplace has:
- Emergency Eyewash Stations: Install eyewash stations near battery charging and maintenance areas to provide immediate relief in case of acid splashes.
- Spill Kits: Keep spill kits readily available to contain and neutralize acid spills. Train employees on how to use these kits effectively.
- First Aid Training: Provide first aid training to employees, focusing on the specific risks associated with battery handling and the appropriate response measures.
To learn more about forklift batteries and battery safety programs, contact a Power Solutions expert at Associated today.
__________________________________________________________________________
Founded in 1960, Associated provides a single-source solution covering the manufacture, design, integration, and service of your equipment—everything from forklifts and conveyors to automation and pallet handling systems. Associated has the ability to enhance the efficiency, reliability, and productivity of their customer’s operations with the most complete intralogistics capabilities in the industry. Associated is an Authorized Raymond Solutions and Support Center. For more information or to discuss your Material Handling project needs, please visit www.associated-solutions.com or contact us at:
[email protected]
(800) 755-7201
___________________________________________________________________________