By Making Your Battery Room OSHA Compliant
Making Your Battery Room OSHA-Approved
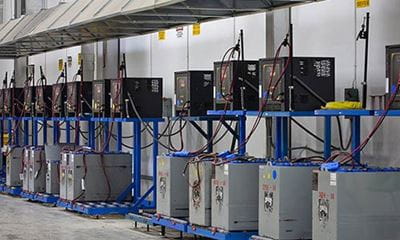
Every warehouse or plant that uses electric forklifts on site will have a designated room or area where batteries are stored.
Sulfuric acid will destroy the floor and even soften concrete over time. Worse yet, it will burn through an employee’s clothing and possibly cause serious burns and other related injuries, such as infection.
If a spill occurs, the solution is to sprinkle a neutralizing acid absorber on the sulfuric acid. The powder acts like cat litter by soaking up the spill. Despite its effectiveness, many warehouses don’t keep this product on site.
Sometimes, sulfuric acid can splash on an employee’s face or body. Warehouses must have eye wash stations that are less than 25 feet from the battery room or area, according to OSHA. The stations usually consist of a shower or water fountain with two streams, enabling both eyes to be rinsed out at once.
Many employers also store protective gear in their eye wash stations. This includes face shields, goggles with side shields and an acid resistant apron and gloves, which are often included in a kit.
By creating a compliant battery room or area, you will ensure employee safety, maximize the life of batteries and improve your warehouse’s overall efficiency.