Improving Operational Safety by Identifying the Cause of Accidents
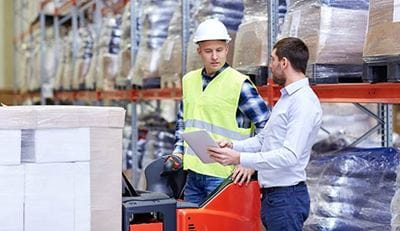
Making sure your employees are safe is a primary focus issue for all employers, and running a facility that operates industrial equipment can add a whole new set of safety concerns.
How many workers are injured each year as a result of forklift misuse? We could say “too many,” but to be precise, the total number of injuries per year (non-serious, serious, and fatal) is 96,785. That’s right, nearly 100,000 workers are injured per year due to improper training or sheer carelessness on the job.
Compared to the estimated number of forklifts in the United States (855,900), that means that each year, more than 1 in 10 forklifts are involved in an accident (assuming 1 accident per forklift). That equates to an accident happening almost every 6 seconds!
So how can Operations Managers help prevent these types of accidents from occurring? Training is the obvious answer. It has been a federal law since 1969 that all operators be trained and evaluated prior to operating a lift truck, yet the number of accidents continues to rise. Although training is the first course of preventative action, to truly improve safety in your environment you must also be able to correct behavior and make adjustments to potentially hazardous conditions on a continual basis.
But how do Operations Managers always know if their lift truck operators have had an accident, or if a certain area of the warehouse is not safe to operate industrial equipment in? Of course if the accident is severe enough the manager will be informed, but what about smaller accidents that can leave the rack structurally unsound and lead to a catastrophic accident in the future?
Many times, because of the size and number of operators in a facility, the Operations Manager is not made aware of these because it would require the operator or their peers to report it.
The good news is that there are ways to enhance operational safety that help to address individual behavior as well as environmental conditions, such as the use of telematics and maintenance-cost monitoring.
Telematics is a way of monitoring the movements, status and behavior of a vehicle and its operator. This information gives management complete, real-time knowledge of their fleet activities in one centralized interface. Many Operations Managers have looked to this technology to provide them with more data to gain insights on their operations, in the form of devices that are mounted on each forklift truck in their fleet. These truck-mounted devices record key data events and transmit them to a database where reports can be retrieved.
Using a telematics system means an Operations Manager can be notified at the exact time an accident occurs. This information will tell them who was operating the forklift and at what velocity they struck something. This information not only allows management to address the behavior of the operator right when it happens, it can also provide them with analytics to review trends per driver or type of truck.
While this information is a tremendous resource in the goal of improving safety, it doesn’t necessarily give you the entire picture. You will know when a forklift was in an accident, but you won’t necessarily know how much cost was incurred as a result of it. Although you can’t put a price on safety, it is important to know how much money you are spending on repairs that were caused by an accident. This is where maintenance cost monitoring can help.
Avoidable repairs: Two words that no Operations Manager wants to hear. With material handling equipment typically being the third-highest cost driver in a warehouse environment, having unwarranted expenses incurred that could have been avoided altogether is a sore subject to say the least. For that reason, these types of repairs are the “low hanging fruit” that managers will focus on when it comes to cost reduction.
But what about the impact on safety? Wouldn’t it be great if the type of avoidable repairs that were occurring could also identify unsafe practices in the workplace? Taking that a step further, what if an avoidable repair could help identify unsafe areas in your facility? The truth of the matter is that they can.
By identifying root causes for avoidable repairs, determinations can be made which identify both safety concerns, giving us the ability to make necessary changes in operational procedures and the facility itself, creating a safer environment for all. This method comes with its limitations as well. Unlike with telematics you may not know an accident occurs until weeks after the incident. Also, depending on how you assign your forklifts, you may not be able to determine exactly who was the driver at the time of the accident.
The unfortunate truth is that accidents will happen, and ultimately to achieve a high level of safety there is not one magic bullet. However by utilizing a combination of training, telematics and maintenance-cost reporting you can help ensure these accidents happen less frequently, with fewer injuries and at a lower cost.